April 9, 2006
In this topic:
Page 1
Page 2
- The Kingsford Testing Protocol
- Old Versus New Kingsford Temperature Curve
- WSM Minion Method Temperature Curve
- My Minion Method Demo
- Using New Kingsford For Low & Slow Barbecue
- What’s In The New Kingsford?
- How New Kingsford Works
- Common Complaints About Kingsford
- Miscellaneous Items
- More Information About New Kingsford
- More Kingsford Links On TVWB
Purpose Of My Visit
At the end of 2005, a new version of Kingsford Charcoal Briquets began to appear on store shelves in the United States. Much discussion about the new product was posted on The Virtual Weber Bulletin Board, some of it saying that new Kingsford did not burn as long as old Kingsford when used for overnight cooking.
This discussion caught the attention of the folks at Kingsford. Kelly Burke, a scientist with the Kingsford R&D group, contacted me to ask if we could meet to discuss the bulletin board feedback.
On Sunday, April 9, 2006, I visited the Clorox Technical Center in Pleasanton, CA. I was hosted by Kelly Burke and Bob Miller, the R&D manager for Kingsford Charcoal Briquets.
The purpose of my visit was to:
- Demonstrate the way I use the Minion Method to fire the Weber Smokey Mountain Cooker using Kingsford Charcoal Briquets.
- Discuss the complaints about new Kingsford by members of the bulletin board.
- Tour the product testing facility to learn how Kingsford applies scientific processes to the testing of their products.
Purpose Of This Article & Disclosures
The purpose of this article is to share what I learned during my visit. I have not written this article to defend Kingsford against negative publicity, or to change anyone’s opinion about the new product, or to promote it. Kingsford did not tell me what to write about in this article, but they did review it prior to publication to make sure that no company confidential information was revealed.
TVWB has no vested interest in the charcoal product you use, Kingsford or otherwise. TVWB is not sponsored by or affiliated in any way with The Clorox Company or Kingsford Charcoal Briquets. I did not receive any financial compensation, nor did I receive any free product, in exchange for this article.
In the spirit of full disclosure, I must report that I enjoyed eating 4 steak skewers, seasoned with salt, pepper, granulated garlic powder, and onion powder, that Kelly grilled on a Weber kettle in the test lab. They were juicy and delicious.
About The Clorox Technical Center
The Clorox Technical Center in Pleasanton, CA employs about 500 people involved with research, development, and testing of all Clorox products. These include such well-known products as Clorox bleach, Pine Sol, Tilex, Formula 409, Glad plastic bags and containers, Armor All protectants, STP oil additives, Fresh Step kitty litter, Brita water filtration, Hidden Ranch salad dressings, and most important to barbecue enthusiasts, KC Masterpiece barbecue sauce and Kingsford charcoal.
The Briquette Pilot Plant
I arrived just before 11:00am and was met by Kelly at the main lobby. He escorted me though the building to the Kingsford testing facility, which is just a small part of the large campus-like complex. We were joined later that morning by Bob Miller, the R&D manager.
Once I was outfitted with a pair of safety glasses, Kelly took me into the briquette pilot plant where experimental batches of briquettes are produced for R&D purposes. We climbed a flight of stairs to an elevated platform where a batch mixer resided. Imagine sort of a barrel on its side with horizontal mixing blades inside and an access door on top.
Dry ingredients and cooked corn starch as a binder are combined to create “green mix”, a wet briquette material that’s similar in consistency to snow in the sense that it can be compressed without dripping any water.
Since the R&D lab does not have the ability to produce wood char in-house, this ingredient—the most abundant in the product—is shipped in from one of the regional factories.
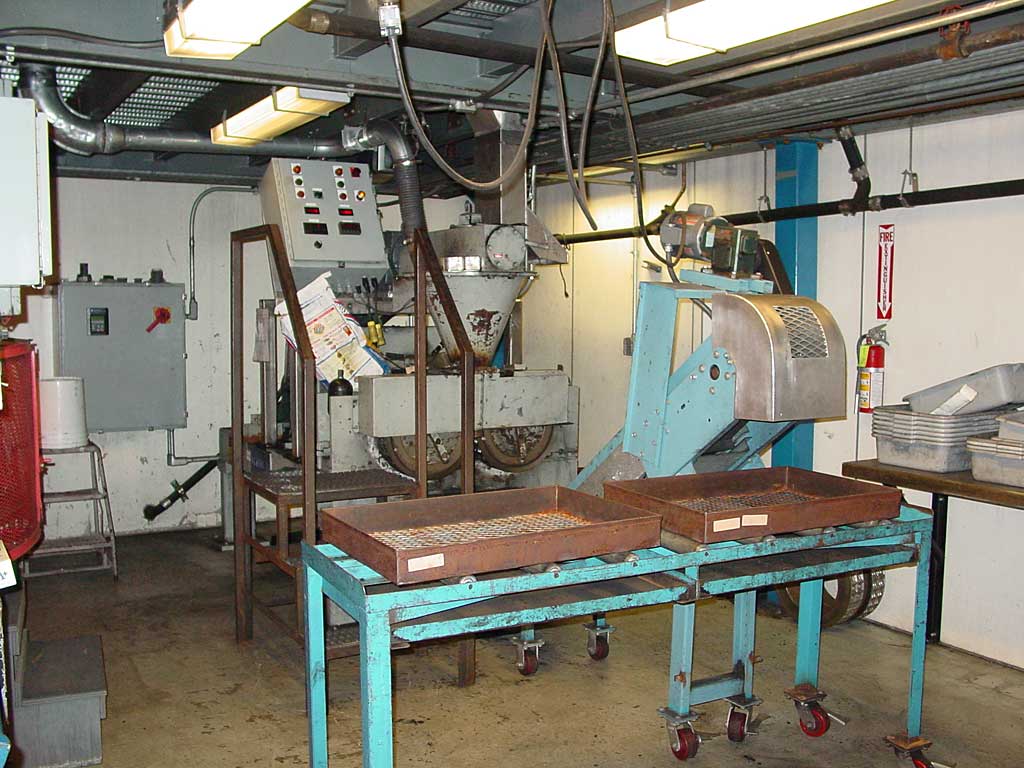
The R&D briquette press. Much larger machines are used to make briquettes at regional production facilities around the United States.
The green mix is conveyed downstairs to a briquette press. The mix flows into the spaces between two rotating press rolls, forming the pillow-shaped briquettes. One wheel makes the “K” imprint on the front, the other wheel makes the two Sure Fire Grooves on the back.
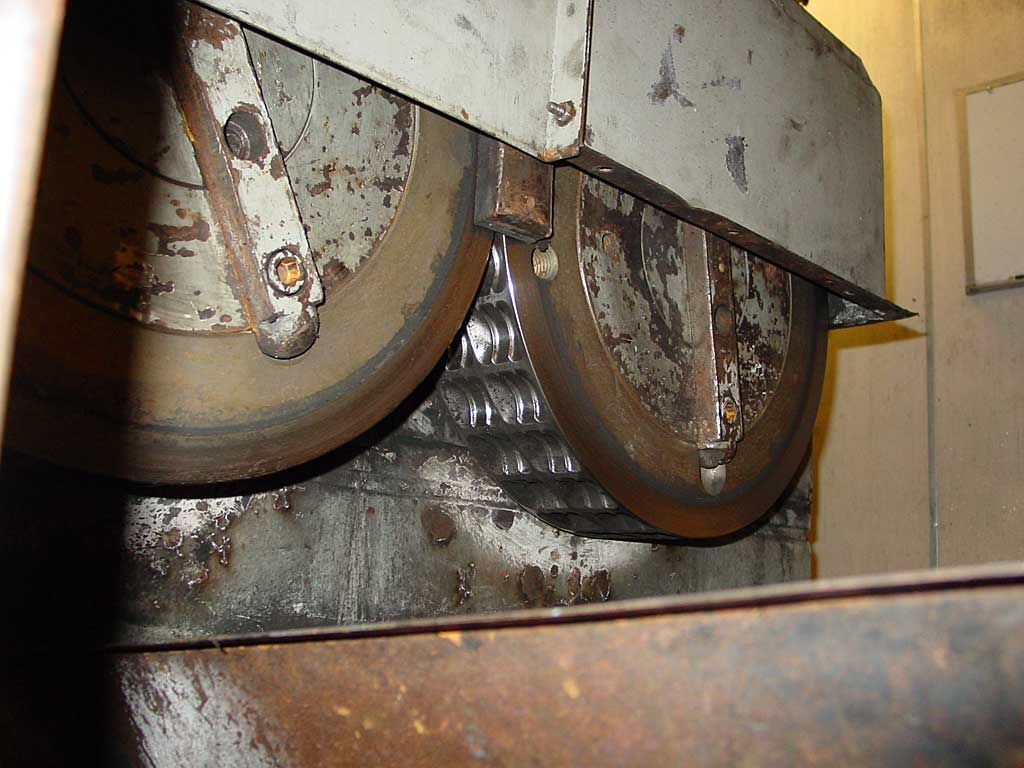
Rotating press rolls form two briquettes side by side. The wheel on the right makes the Sure Fire Groove impression.
The “green briquettes” are conveyed to steel trays made of expanded metal. Loose bits of material and rough edges called “fines” are knocked off the briquettes and fall through the bottom of the trays.
The trays are loaded onto racks and rolled into a drying chamber to remove moisture and set the product shape. The finished briquettes are then cooled and bagged, ready for use in the R&D test lab or for shipment to customers around the country that participate in field testing of Kingsford products.
The Climate-Controlled Charcoal Storage Room
Adjacent to the briquette pilot plant, behind a heavy sealed door, is a separate temperature- and humidity-controlled room where a large quantity of Kingsford products is stored. These products are allowed to stabilize in this room for a period of time before being used in the test lab. Bags of charcoal are stacked on ventilated wire shelves, and small plastic bins hang off the wall containing production samples from Kingsford factories around the United States.
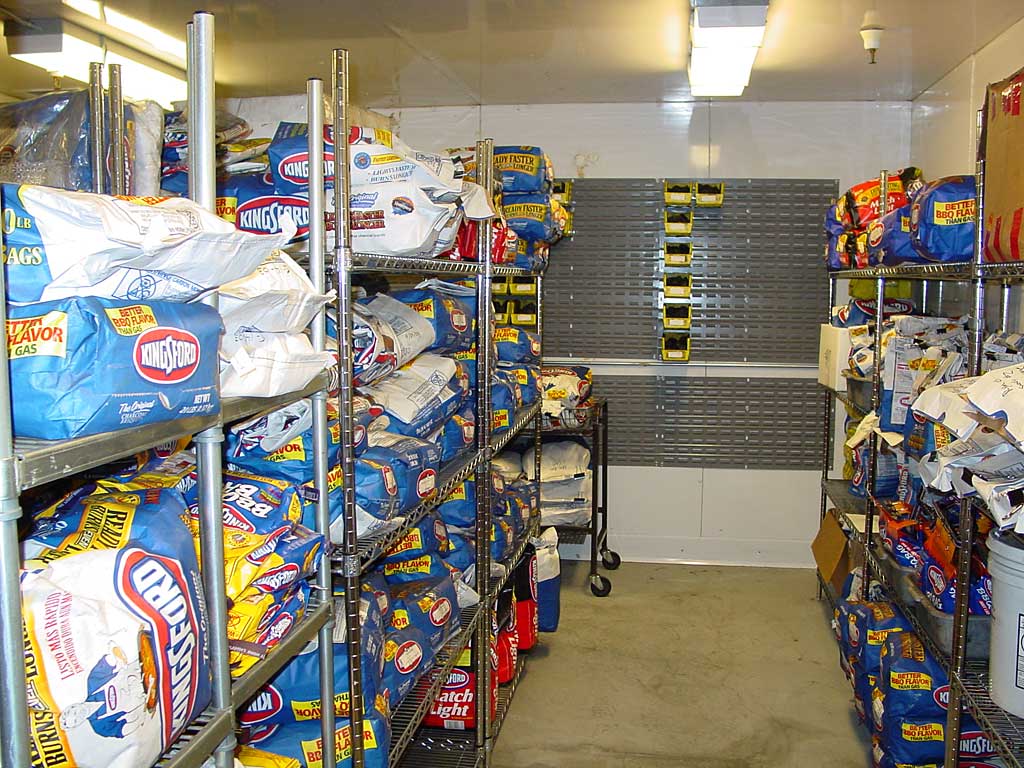
Kingsford and competitive products are stored in this climate-controlled room prior to testing. The yellow bins on the back wall contain sample briquettes from factory production runs. There were many more of these bins in other parts of the room. This photo shows half of the entire room.
I also saw a variety of competitive products stored in this room. Each year, Kingsford tests their product against all branded and private-label charcoals from the top 20 charcoal markets in the country.
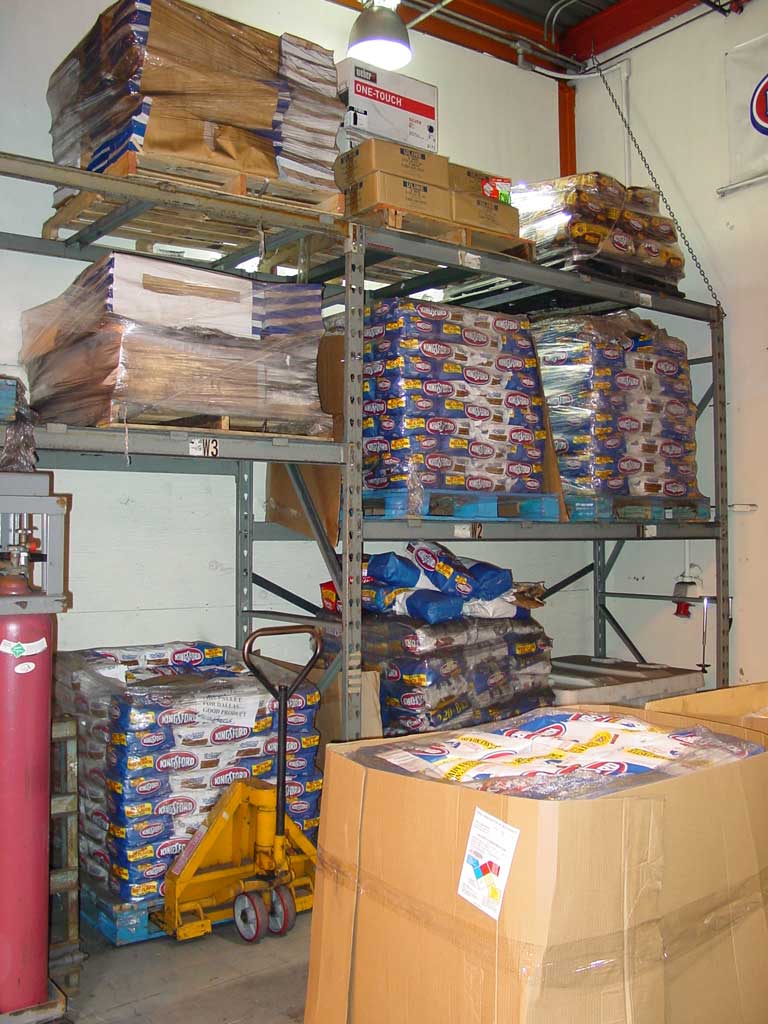
Pallets of old and new Kingsford are stored in the warehouse adjacent to the testing lab. Notice the Weber kettle box on the top shelf.
The Weber Burn Room
The next stop on my tour was the Weber burn room, where a WSM was already setup and waiting for my Minion Method demo. I’ll tell you more about that a bit later in this article.
This room consists of 8 test stations, 4 on each side of the room. Each station consists of a three-sided enclosure, open on the front, with a concrete floor below and a ventilation hood above. In the center of each station is a 22-1/2″ kettle bowl and ash catcher attached to a pivoting frame for easy dumping of ashes. This setup is meant to mimic the way a customer might use Kingsford for high-temperature grilling in the backyard. In the corner of the lab was an industrial-strength, fire-proof ash disposal bin with ventilation to the outside.
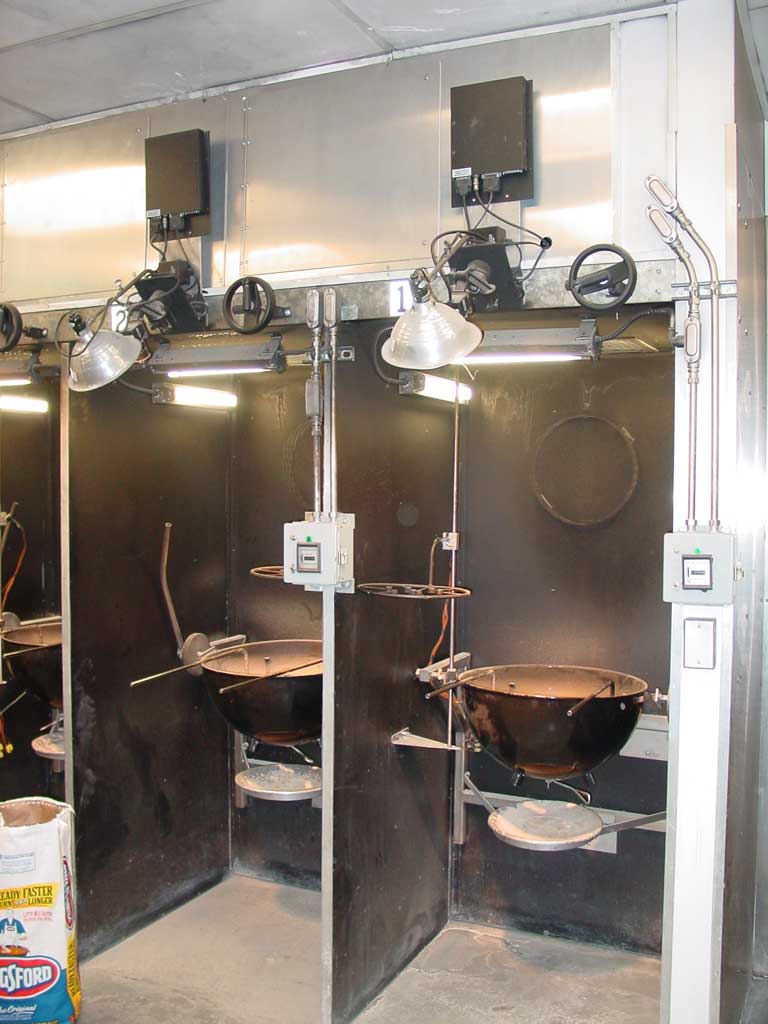
Test stations in the Weber burn room. A charcoal ring hangs on the back wall. The circular thermocouple array is shown about 12″ above and to the left of the kettle on the right. The gray box outside each station is a timer. The black box above each station is an interface that connects test equipment to a monitoring computer.
To conduct a burn test, a measured amount of briquettes is placed in a wire ring on the charcoal grate and a measured amount of solvent (lighter fluid) is applied and lit. A circular array of 7 thermocouple probes is placed at grilling height above the fire and the readings are tracked by computer. A timer at each station tracks burn time, and other proprietary technology is used to monitor product performance and is tracked by computer. All 8 stations can be monitored simultaneously by a single Apple desktop computer.
The Division Lab Burn Room
In a separate, larger room is the division lab burn room. This room contains 16 stations, 8 on each side of the room, with a large work area running down the middle. Each station consists of a fireplace insert installed waist-high in the wall and ventilated to the outside by an exhaust fan.
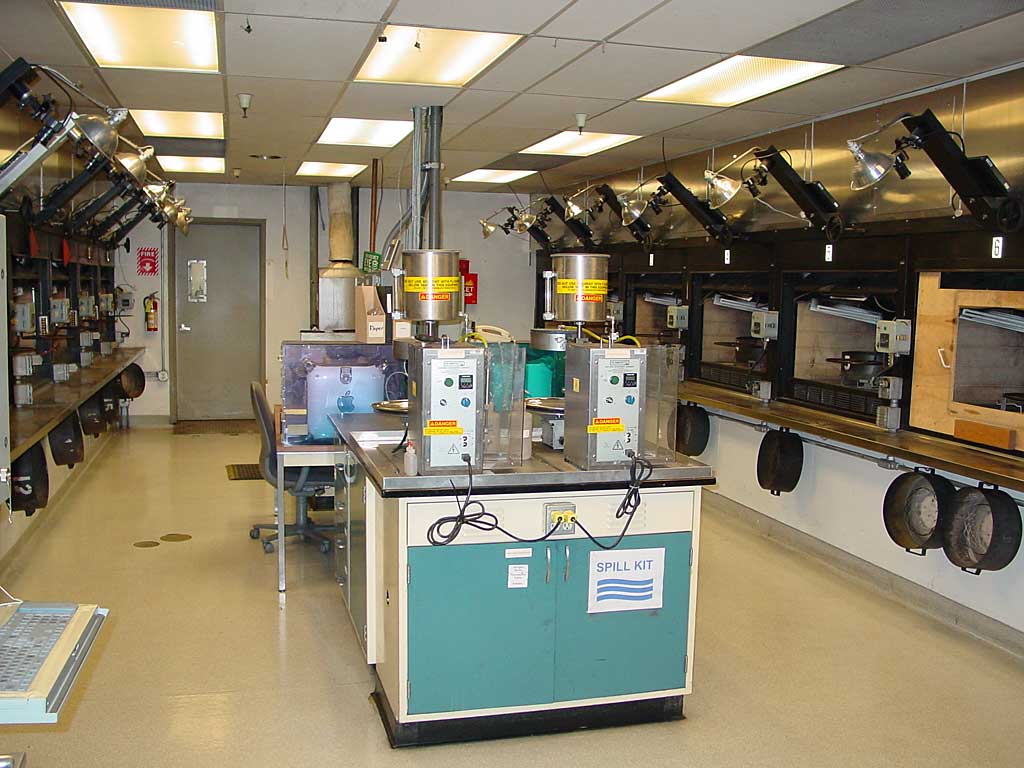
The division lab burn room. The two machines on the table in the foreground apply a measured amount of solvent to each charcoal sample prior to lighting. Charcoal rings are seen hanging below each test station. Not shown in this photo is a special test station that burns charcoal on a scale so weight can be measured throughout the burn test.
Unlike the Weber burn room, which is designed to mimic customer usage of Kingsford, the division lab burn room conducts scientific “stress tests” of charcoal products to determine their performance characteristics.
As in the Weber burn room, a measured amount of charcoal is placed in a metal ring, a measured amount of solvent is applied, and the charcoal is lit and burned. The same setup of thermocouples, timers, and proprietary technology is used to track the burning charcoal by computer.
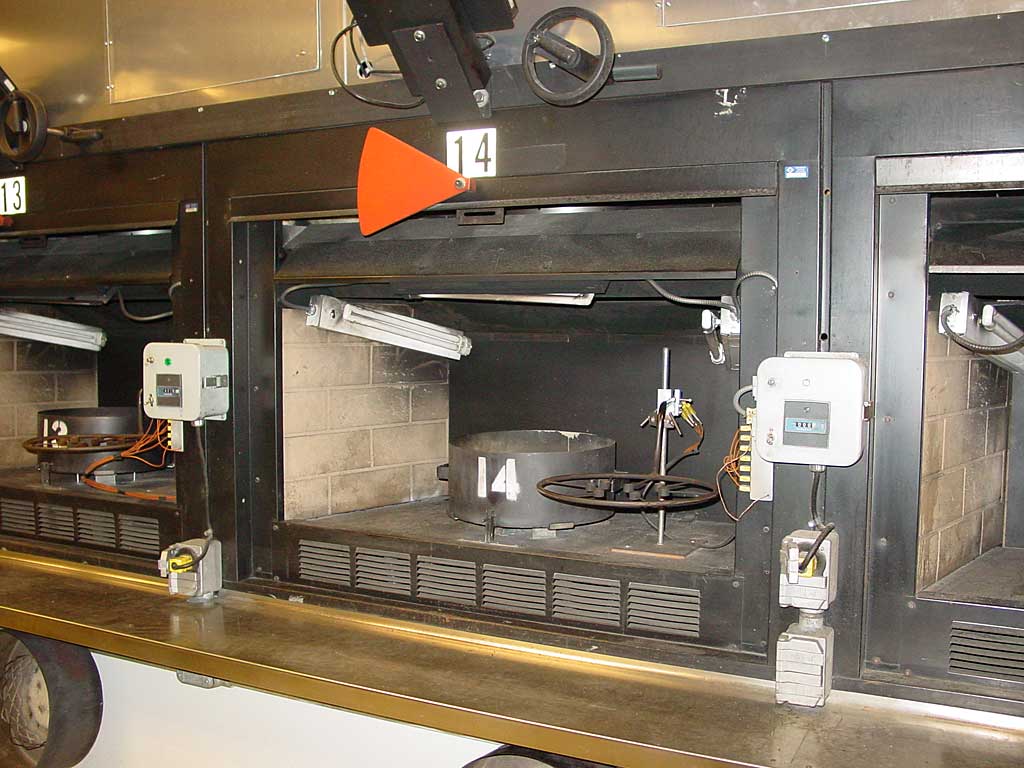
Close-up of test station #14. This photo offers a better view of the circular thermocouple array to the right of the charcoal ring. The white box to the right is a timer.
These labs runs thousands of burn tests each year for a variety of purposes. “Here we separate the men from the boys,” said Kelly, by evaluating the performance of production Kingsford against prototype products and competitive products. They also run tests of production samples from the various factories around the United States for quality assurance purposes.